If you are looking for the right design and manufacturing partner for your cleantech or greentech project, we are here to serve you.
Case Study: CarbonCure Technologies: Making Concrete More Sustainable
This case study first appeared in Soracom’s website and has been published here with permission from Soracom and CarbonCure.
Concrete is the most widely used substance in the world, after drinking water — but the realities of the manufacturing processeses for cement, concrete’s key ingredient, also make it a major source of carbon emissions. One study found that if the cement industry were a country, it would be the third-largest greenhouse gas emitter in the world behind China and the United States. Of course, the world needs concrete for dense, walkable roadways, and safe, strong infrastructure developments that can resist climate change, so finding a smarter path to concrete creation is essential.
Founded in 2012, Nova Scotia-based CarbonCure Technologies has developed a system to reduce the carbon footprint of concrete. Its technologies inject a precise dosage of captured carbon dioxide (CO₂) during the concrete manufacturing process, where the CO₂ immediately mineralizes and becomes permanently embedded within the material. This mineralization also improves the concrete’s compressive strength, enabling reductions in cement and its associated carbon emissions. It’s a win-win for sustainability.
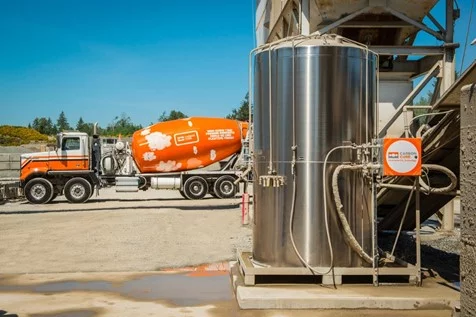
Challenge
Examine the entire lifecycle of concrete through hardware
CarbonCure’s goal is to reduce and remove 500 million metric tons of carbon dioxide from the atmosphere each year. To date, the company’s network of concrete producer customers has delivered about 3.5M truckloads of CarbonCure concrete, saving more than 226,000 metric tons of CO₂ emissions since its founding. With visibility into the concrete lifecycle, CarbonCure can reduce emissions at every point.
“This perspective allows CarbonCure to examine the entire process and pipeline of concrete development to identify potential for efficiency in terms of reducing the carbon footprint of concrete,” said CarbonCure Sr. Director of Engineering Brad Vickers.
CarbonCure’s equipment can be retrofitted into a concrete plant in just one visit. The CarbonCure Valve Box connects to the CO₂ tank stored onsite and automatically injects a precise dosage of CO₂ into fresh concrete or reclaimed wash water collected during plant operations. The Control Box then syncs with the plant’s batching software, allowing users to stay up to date on the manufacturing process as it moves forward.
“It’s a process that needs continuous innovation and deployment of hardware and software solutions,” said Vickers.
Solution
Build a stream of telemetry data
Recognizing that a technological solution was needed, and aiming to enhance the products produced in-house, CarbonCure sought external support to help perfect its unique management system, ultimately finding a fitting match with Ontario-based design firm NeuronicWorks.
“The CarbonCure system’s design was improved, certified, and manufactured by working closely with NeuronicWorks,” said Vickers.
“We were approached by CarbonCure with this innovative concept and were thrilled to collaborate with their team to create a scalable, distributed solution. As a company, the GreenTech space is a key priority for us, and this was the perfect opportunity to do our part and support CarbonCure’s mission to reduce the carbon footprint of concrete” said Titu Botos, CEO and Co-Founder of NeuronicWorks.
Working together, the organizations designed a distributed wireless system (dubbed the Control Box), made up of a central unit that can control and gather data from several field units (called Valve Boxes) that are daisy-chained over serial communication. The field units are installed close to the concrete mixing equipment, controlling the process, and gathering real-time operational data.
Each Control Box gathers telemetry data and syncs with a CarbonCure command center in real time. CarbonCure staff maintains the technology’s 99% uptime and remotely administers ongoing support with quick response times.
“We can easily see the status of the device, ensure that everything is working correctly, and monitor injection status,” Vickers said. “Seeing how much CO₂ goes into every batch of concrete, we can generate high quality carbon credits. Using the data coming in from the injections matched with batching data, we can analyze the mix design for its efficiency.”
CarbonCure’s reference projects include Amazon HQ2 in Arlington, VA, the LinkedIn Middlefield Campus in Mountain View, CA, the Infosys Technology and Innovation Hub in Indianapolis, IN, and more.
One of CarbonCure’s immediate-term goals is to become a worldwide solution. The pursuit of this milestone is crucial to the future of the reduction of carbon emissions.
Why NeuronicWorks?
End-to-End Product Design and Manufacturing under one roof
NeuronicWorks was tasked with designing and developing a fully functional, assembled, and tested system for controlling the concrete manufacturing process.
“With both design and manufacturing services housed under one roof, it becomes easier for our clients like CarbonCure to closely work with our team without the general interruptions and delays commonly experienced working with multiple vendors,” said Botos.
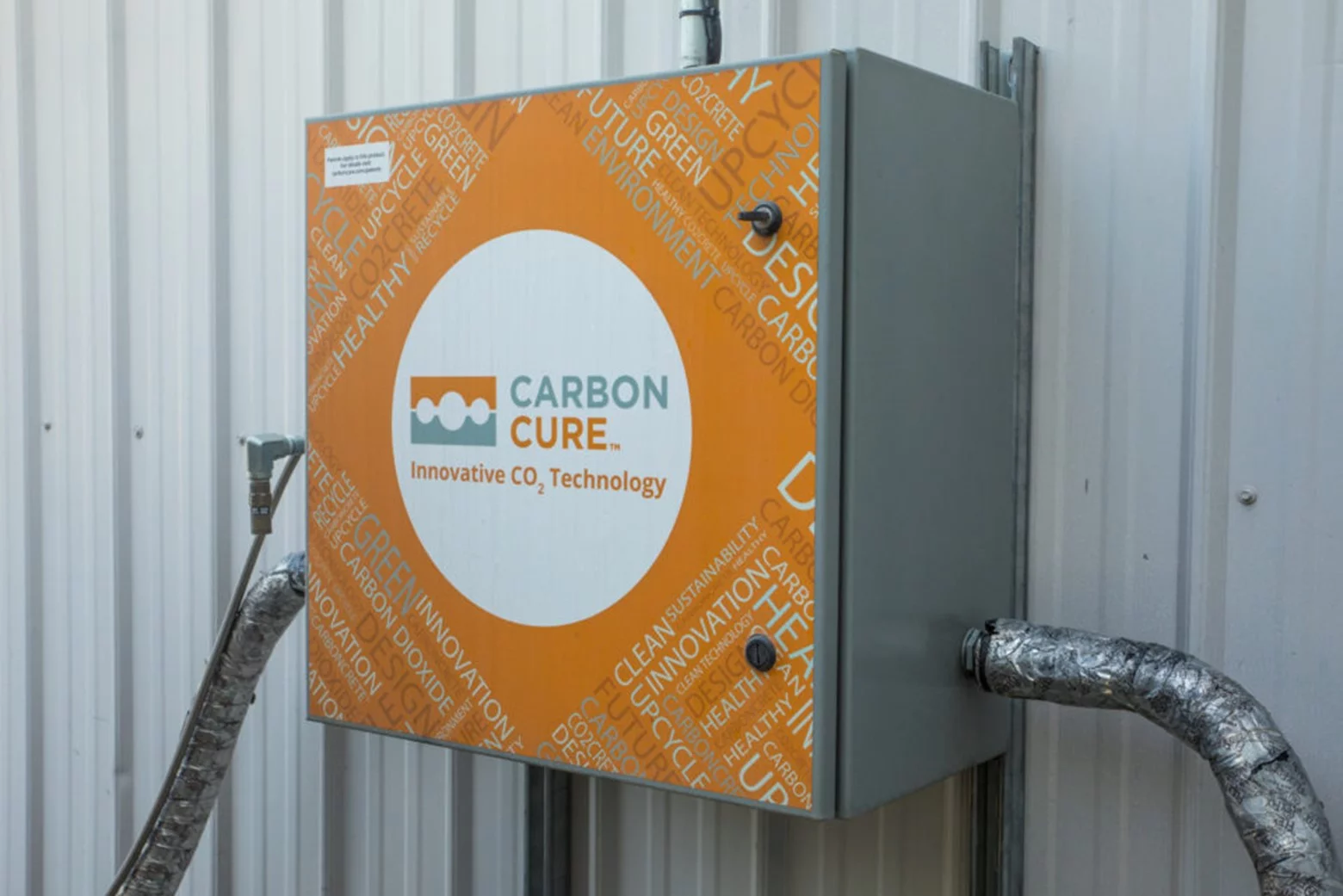
The NeuronicWorks’ design team contribution ranged from Firmware design to Industrial and Mechanical Design, also offering pre-certification support for the entire system. The team reviewed and updated existing hardware and utilized a bare metal approach for firmware development, ensuring the system was set up for OTA updates and communication with the cloud backend for seamless operation.
“We continue to work closely with CarbonCure providing onshore design and box build services that meet the North American safety and quality standards, for a complete turn-key service” said Botos.
Why Soracom?
Unparalleled security, coverage, and tech
Cellular connectivity is essential for gathering telemetry data, particularly from remote sites that don’t have internet.
“We needed a way for devices to communicate with a server, bidirectionally and securely,” said Vickers.
The CarbonCure engineering team conducted an exhaustive search, speaking directly with SIM card providers, mobile network operators, and other connectivity solutions. Despite those efforts, however, CarbonCure was unable to find a solution that had the right mix of global coverage and security, along with the ability to directly communicate with a server.
It was a conversation with their design and manufacturing team at NeuronicWorks that would introduce them to Soracom.
“NeuronicWorks had worked with Soracom in the past and pointed us to the company,” said Vickers. “[They] said that the experience was great.”
In addition to connectivity, Soracom’s suite of value-added services has helped enrich the security of CarbonCure’s technology stack. Chief among these solutions is the IoT protocol conversion tool, Soracom Beam.
Outcome
World-changing technology
More than 28 million cubic yards of lower carbon concrete have been delivered by CarbonCure and its concrete producer customers. In April 2021, it was announced that Team CarbonCure won the Carbon XPRIZE, which was a global, 54-month competition that challenged participants to develop breakthrough technologies to convert CO₂ into a usable technology. In addition, CarbonCure was featured on the 2022 CNBC Disruptor 50 List and inducted into the Cleantech 100 Hall of Fame. The company has also supported some of the most high-stakes construction projects in North America.
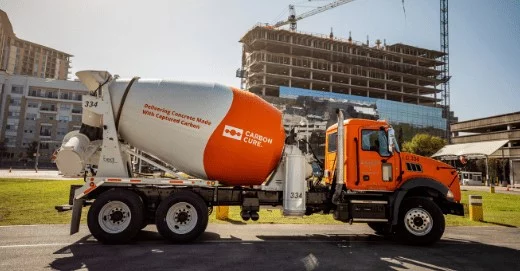
With an already-powerful track record, CarbonCure is scaling globally with systems sold across more than 30 countries. It is a commitment to continuous experimentation and rapid evolution that pushes the company forward.
“There’s a lot of potential to build infrastructure that helps CarbonCure scale past our existing PLC solution and create options to help both smaller and larger concrete producers become more sustainable,” Vickers said. “The solution we have is strong — but we are always iterating upon it to fully maximize its potential. It’s about continually solving challenges and ensuring we have the hardware and software infrastructure to keep evolving.”