We have been around the block a couple of times over the years and know what it takes to bring a product to market. Let us help you with your product design, prototyping and manufacturing requirements today.
Points To Consider When Choosing An Electronic Product Design and Manufacturing Firm
Product design and development services offered by design firms can range from full-fledged end-to-end services to executing a specific task that is part of a larger project. Here are some common scenarios where a product design firm is the solution:
1: You have a great product idea and now want to see it realized into a few prototypes, but you aren’t sure where and how to start.
2: You are in the middle of a great project, but you come across a few technical obstacles that are beyond your professional scope. The project is stalling, and you need help stat.
3: You are planning a long-term, high-architecture project and are looking to outsource some of the services required to a design partner with the right strengths.
This is where the services of a design firm can bring in true value.
Outsourcing electronic product development can reduce costs, timeline and risks and increase efficiency. Some of the main reasons for outsourcing development are a lack of internal resources including manpower and specific experience and expertise.
Electronic design is a broad discipline with several niche areas – hardware design, firmware design, software development, industrial design, mechanical design, UX/UI design, prototyping, testing and certification, manufacturing, among others. An ideal design firm is one that offers all these key services in-house in an integrated form, maximizing seamless collaboration and minimizing risk of miscommunication.
With this perspective, let’s look at some of the factors to keep in mind while choosing the right design partner for you:
1. Experience & Expertise
Choose a design firm that has a considerable number of years designing projects of varying sizes and for various industries. With years of experience, comes well defined processes and fool-proof action plans that are crucial to the success of a project. Evaluate the product development process of the design firm you are contemplating and ensure their process map meets your requirements.
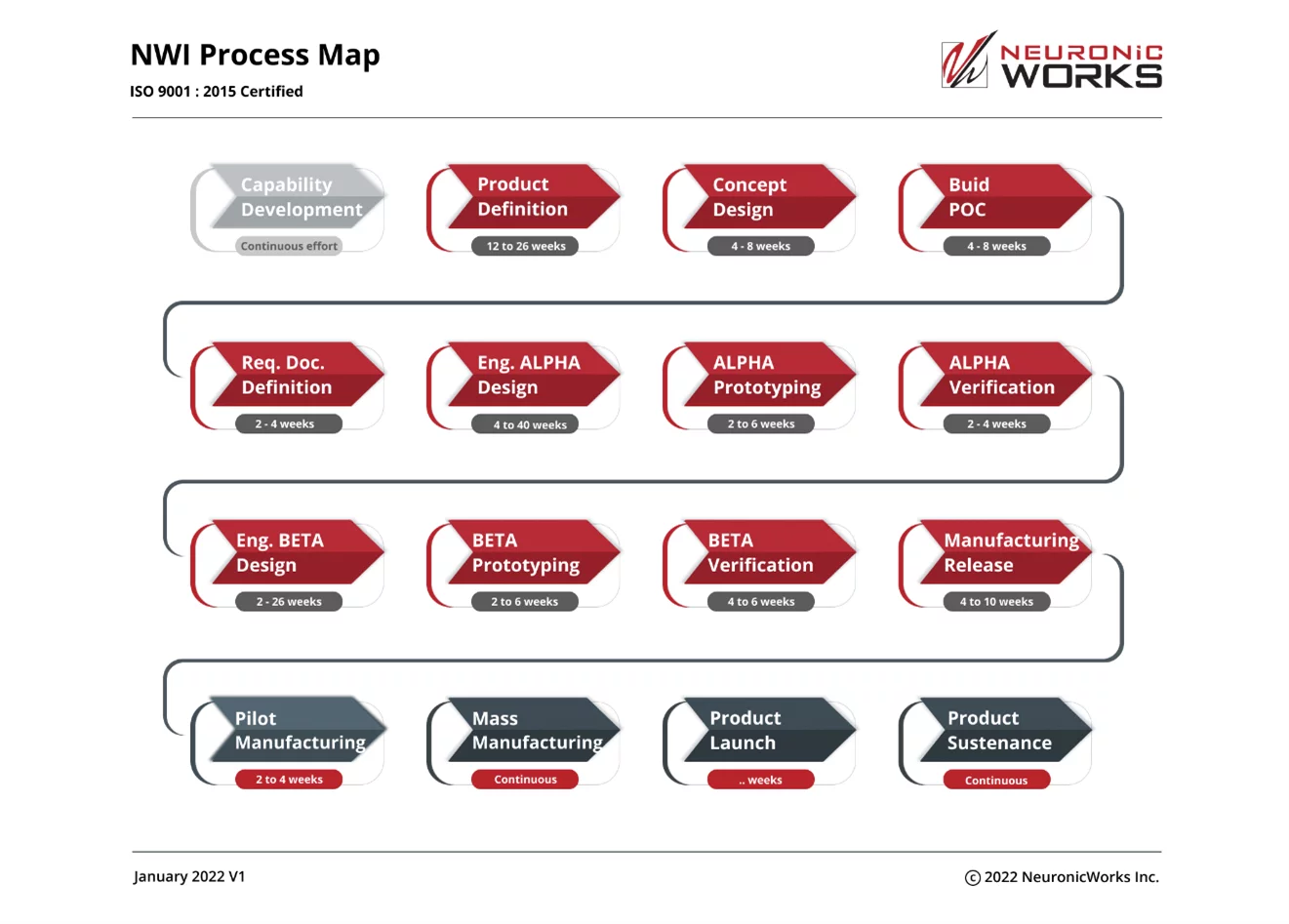
Figure 1: NWI Process Map
Keep in mind to check on both the experience of the firm and the experience of the team. Understand if the team comprises of members with specific domain knowledge. Remember that products can range in complexity from a simple lighting device to complex robotics and while firms may claim expertise in product design and development, dig deeper to understand the range of complexities depending on your application.
Also look for the various tools, software packages, equipment and instruments the design firm houses to get an understanding of their experience. Depending on complexity, some projects may require dedicated facilities such as clean rooms or thermal chambers, check if the design firm has such facilities in-house or at least has established, proven partners to offer such facilities. Using such facilities from a third-party firm could result in an additional cost that will have to be considered as part of the project budget.
Remember that an experienced design firm will be able to quickly understand your requirements, translate them into achievable objectives, foresee challenges and employ strategies to overcome them while delivering quality projects.
2. Standards and Certification expertise
While regulatory certification may seem like a task that can be left to the last minute, this is far from the truth. Regulatory certification requirements need to be considered very early on in the decision-making stage. Without the proper certifications, you may not be able to market or sell your product. Acquiring the proper certifications requires that you pass certain tests.
It is imperative that there be a business plan which outlines the markets where the product will be sold, and the timelines for reaching these markets. This allows a design firm to plan and design according to the required regulatory standards. If you don’t consider certification when thinking about your product development, you greatly increase the risk of the entire business of that product failing and losing a lot of money in the process.
You can read more about certification requirements in our blogs on Understanding Certification Requirements for Electronic Devices and Preparing for certification: Product Development.
An experienced design firm will have a standards and regulatory certification team that can provide important insights on the various certification and standards the product will have to comply with.
Comprehensive test strategies should be concurrently developed with the product design plan to ensure best possible test coverage and product success. Make sure your design firm will have strong partnerships with accredited testing laboratories to make the testing and certification process as efficient as possible.
3. Sourcing and supply chain management
Look for a design firm with a consistent history of timely component sourcing and strong supply chain management. Especially in the current market scenario, development times have stretched beyond typical timelines attributable to the global electronic component shortage. The challenge is real, you can read more about this in our blog on Electronic Component Shortages and it’s impact on product design and development.
Design and manufacturing houses typically have better sourcing power because of their long-term relationships with distributors and buying volume. They can help choose optimal components for your design based on cost, lifecycle, availability, and lead times. Make sure the design firm you are contemplating to choose has the right relationships with reputed distributors to leverage this advantage.
4. Project management and communication
Despite the size of the project, once kicked-off, there are multiple personnel working on it at any given time. It is imperative that the design firm you choose has a well-established project management process and strategies in place to ensure seamless communication between the firm and yourself.
Here’s a blog on Project Management in Product Design and Development that can give some insight into the project management process.
Ideally, you should be assigned a single point of contact, an account or project manager, who can deliver updates in a timely manner, gather feedback, measure goals, and ensure consistent communication with the technical team for project success.
Ask about the project management methodology, documentation system, and reporting system, that is being used internally for all projects. Check if the team offers regular stand-up meetings and review meetings and ask if and how they provide a documented plan that tracks the project progress.
5. Vertical Integration
Working with a vertically integrated firm that offers both design and manufacturing services under one roof presents several advantages.
Feedback from the manufacturing team can be incorporated and acted upon earlier on in the design phase which reduces the risk of unforeseen issues and creates a seamless design transfer to manufacturing.
Here’s a blog that shares some insight on the Product Manufacturing: Design Transfer process.
Having the design and manufacturing teams working out of one location, allows for seamless transfer of information between the two teams. For example, if the PCB Assembly team, determines an issue with the PCB design, the design team can immediately get involved to sort the issue, ensuring time saving. On the other hand, if the PCB Assembly is done at a separate location, by a separate firm, maybe in a different geographic location, the delays in information exchange can be quite significant.
Additional considerations
While the above are some considerations that stand out, here are some additional considerations to keep in mind while choosing a design firm:
Geography
Location! Location! Location! Though the world has become smaller with nearly all services delivered remotely across the oceans, sending your projects offshore for design can still come with its own set of challenges – time zone differences, delivery challenges, communication (language) limitations, IP ownership, legal challenges and more.
Having a domestic design partner can make it easier for you to be on top of things: physically visiting the location, meeting with the technical team if the need arises, dropping and picking units or components, among others.
In terms of legal considerations, you may not have the same legal protections as you would domestically. Foreign countries would not be mandated or bound to contracts, warranties, liabilities, and intellectual property rights as you intend to implement and protect onshore. You would need the services of a qualified attorney with experience in international trade and IP protection.
Client Retention
Because of the nature of business and the NDAs involved, design firms usually do not share a list or details of all their clients and projects. They usually can present only a limited portfolio of projects from customers that are willing to share. But that said, it would always be advisable to ask the firm about past and existing customers to gain an understanding of their repeat customers (at least in terms of percentage). If they have a high retention rate, that means they are doing their job right.
Also, it would be prudent to ask for testimonials and references they would be willing to share. They would usually share the references of their most successful customer, but there is still room to receive honest, critical feedback on their design services from past customers. Ask references questions on how the project went, project success status, the team knowledge and expertise, and financials if necessary.
IP rights
To protect your product design details, it is important to work with a design firm who is trustworthy and who will abide by confidentiality agreements. Make sure that you will exclusively own the intellectual property of your design that the design firm will develop.
Though it will be tempting to work with firms or teams that have delivered on similar products in the past, you could be at a disadvantage of tunnel vision when it comes to development and there is also a risk of unintentional infringement of IP. So, its important to ensure the firm has well-defined processes to ensure the team and documentation is well segregated among competing projects.
Quality compliance
Check the firm’s quality policies and accreditation and ensure their processes meet the required standards needed in the engineering and manufacturing industry. Check for ISO compliance standards as that can ensure higher quality assurance. If your project is in the medical device industry, there could be a requirement of compliance with specific standards. Check for this and ask the design firm for these documentation or statements.
While the above list is not exhaustive, it attempts to cover some of the critical considerations to keep in mind while evaluating a design firm for your product development requirements.
NeuronicWorks is a product design and manufacturing company, established in 2009 and based in Toronto, Ontario. We provide end-to-end product engineering and manufacturing services including hardware design, firmware design, FPGA design, software development, app development, UX/UI design, industrial design, mechanical design, prototyping, testing support, qualification and certification, component obsolescence management, PCB assembly, box build assembly and high-mix low-volume manufacturing support.