Learn more about how NeuronicWorks designs differently and how we can go above and beyond to bring your next device to life. Contact us today.
Our Design Process: Working with you
At NeuronicWorks, we provide complete product development services for all your big ideas. As experts in turnkey electronic design, our in-house capabilities—including hardware, firmware, software, mechanical and industrial design, UI/UX, prototyping, manufacturing support, and testing—will take you through the complete product design process, from ideation to full production, with full support at every stage.
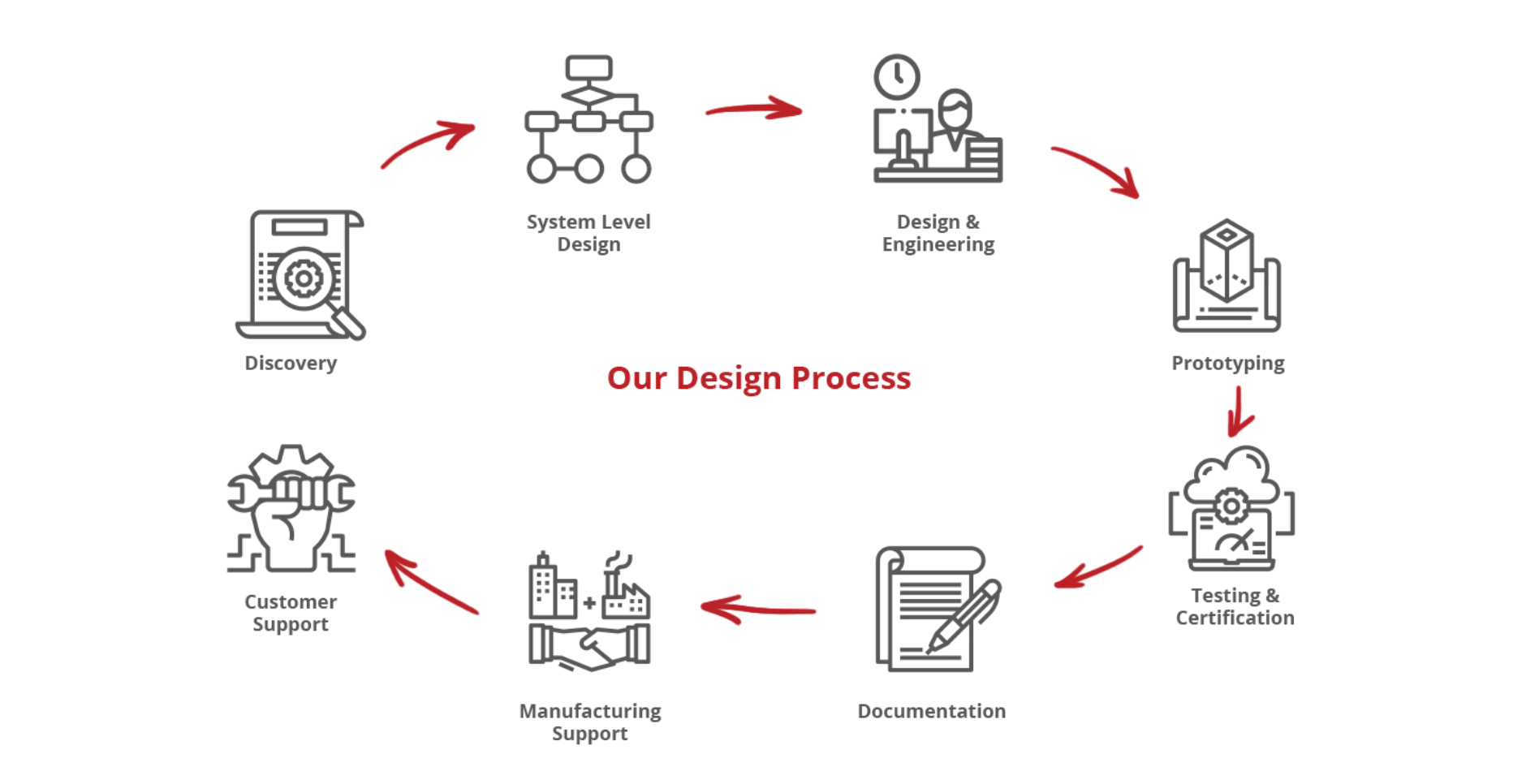
1. Discovery
The crucial first step.
This is our chance to get acquainted with you, our customer, your product, and your market. Establishing this relationship and understanding your needs sets the tone for everything after. We want to understand you, your goals, and have the best sense of what you’re after with each project.
What’s Involved:
•        Deep dive into your product requirements
•        Understanding the end user, market and target price point
•        Understanding your business and its goals, and get the big picture overview
•        Preparing the requirements document that outlines all the product features – it is the keystone for the success of the project

2. System-Level Design
Designing for your market
System-level design follows closely after the Discovery phase and is equally important as it defines the future product. At this stage we discuss your idea with all applicable specialized engineers involved in the project to make sure we have a focused high-level design, and the best technology and processes required to satisfy your product’s needs.
Our multi-dimensional comparative matrix takes dozens of factors into consideration, letting us demonstrate to you that we've worked through all your design needs and that we're choosing the best solution with the fewest drawbacks.
What to Expect:
•        Experienced designers and engineers choose the latest and best tech options for your application
•        Close working relationships with manufacturing partners allows us to select the best components and technologies
•        Partnerships with distributors ensures the availability of parts and their supply chain over the long term
•        Selection of components that aren't near the end of their lifecycle, and that will be ready and available for a long time when it comes time to manufacture the product
Comparative Matrix example
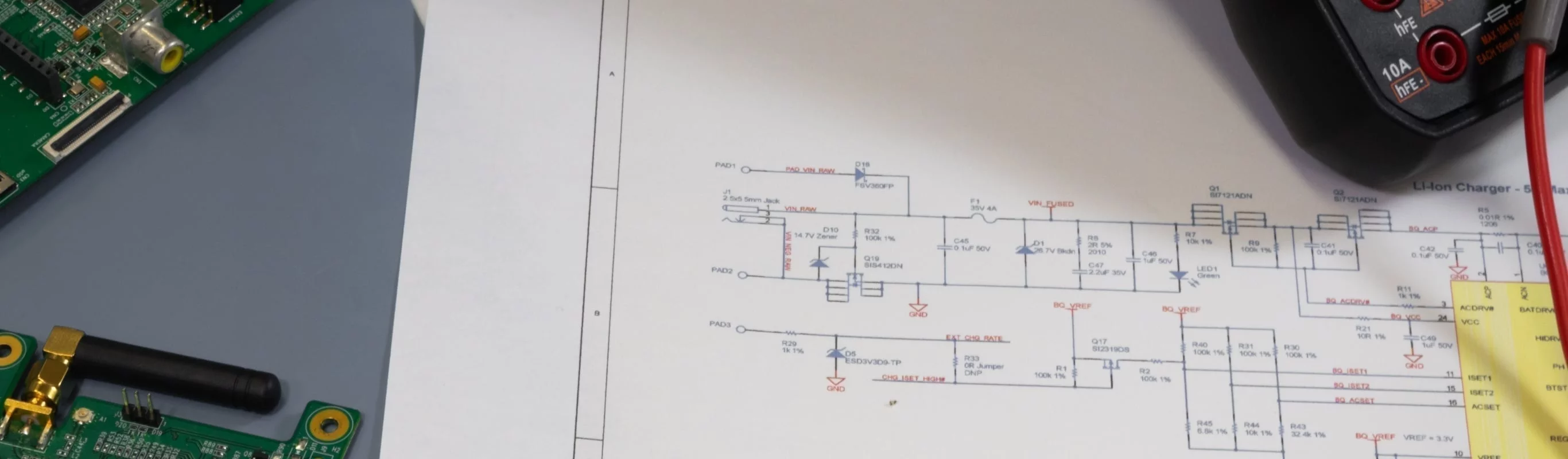
3. Design & Engineering
Our ‘show me’ philosophy
Obviously, we spend the most time on this stage. It's where we bring the skill of our team—everything from hardware design to UI/UX—to bear on the project. We rely on the experience and expertise of our people, our training, organizational workflow, and how we work together to design the best product for you.
What to Expect:
•        We won’t tell you what’s working, we’ll show you what is done
•        Seeing what’s working tells you more about the status of your project than any other update can
•        Knowing everything, you are always in control of the design process
•        Our 11+ years in the industry means we know what it takes to manufacture a product, and we always design for manufacturing
4. Prototyping
See your vision come alive aka feel your product
We want you to have a working prototype in hand as quickly as possible and through the most cost-effective method possible. Once you have something that is working you can refine from there.
What to expect:
•        A working prototype that will help us determine the optimal functionality, test blind spots and adjust features to better address your customers’ needs
•        We will give you the prototype(s) for your own testing, expecting feedback from you
•        We aim to iterate quickly so you can have in the most time and cost-efficient way the final prototype version that will closely resemble the final look and functionality of your product
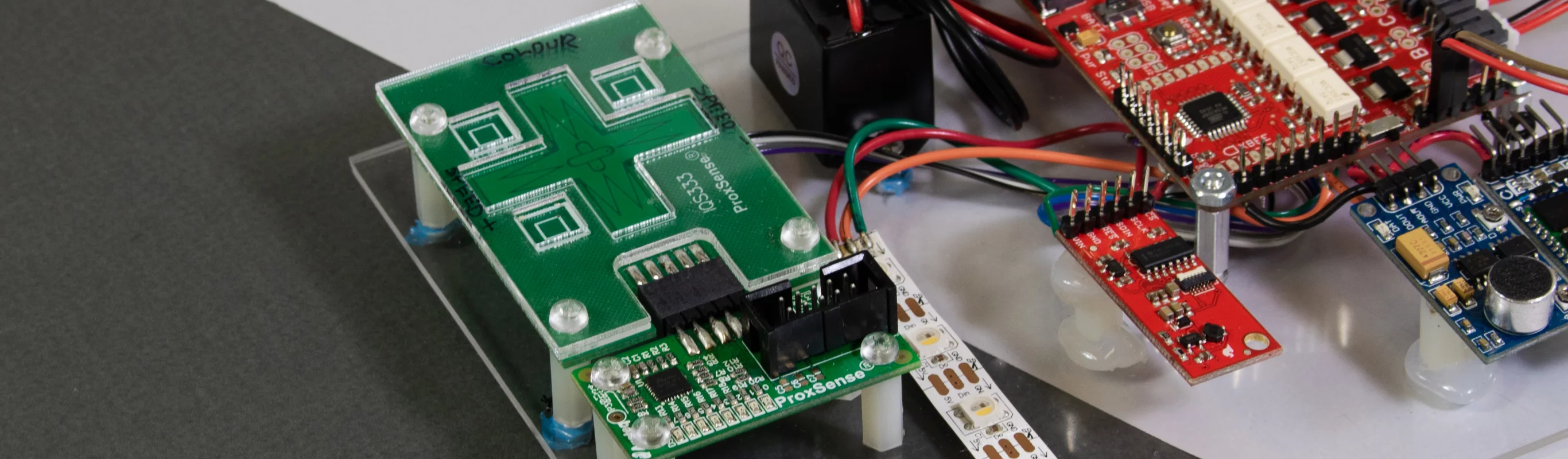
5. Testing, Verification & Certification
Test early, test often
Testing your product through all stages of the development and manufacturing processes is key to ensuring effective performance, product safety, and compliance with the intended quality standards. Our testing process includes functional testing, environmental testing, and safety testing. We test early and often, meaning we know that things are working, and we can proceed with further development.
Our testing & certification process:
•        We do an extensive product testing that includes all system levels (board functions, firmware, mechanical and industrial verification, user experience)
•        The certification testing labs train our engineers directly, making it easier for our people to design and comply with all certification requirements
•        All products go through multiple stages of testing as we home in on peak performance
•        We support you through the certification process to make sure your product complies with the intended industry regulations
6. Documentation
Solid documentation is insurance for the future
We document every step so you and we can retrace our work. Our comprehensive documentation will give you the confidence to pick up the project at any point and keep improving it. We provide you all sources, documents and project history to make sure you don’t miss any important details.
What to expect:
•        All design files we have conceived for you, neatly organized in a tree-like folder structure
•        All manufacturing data
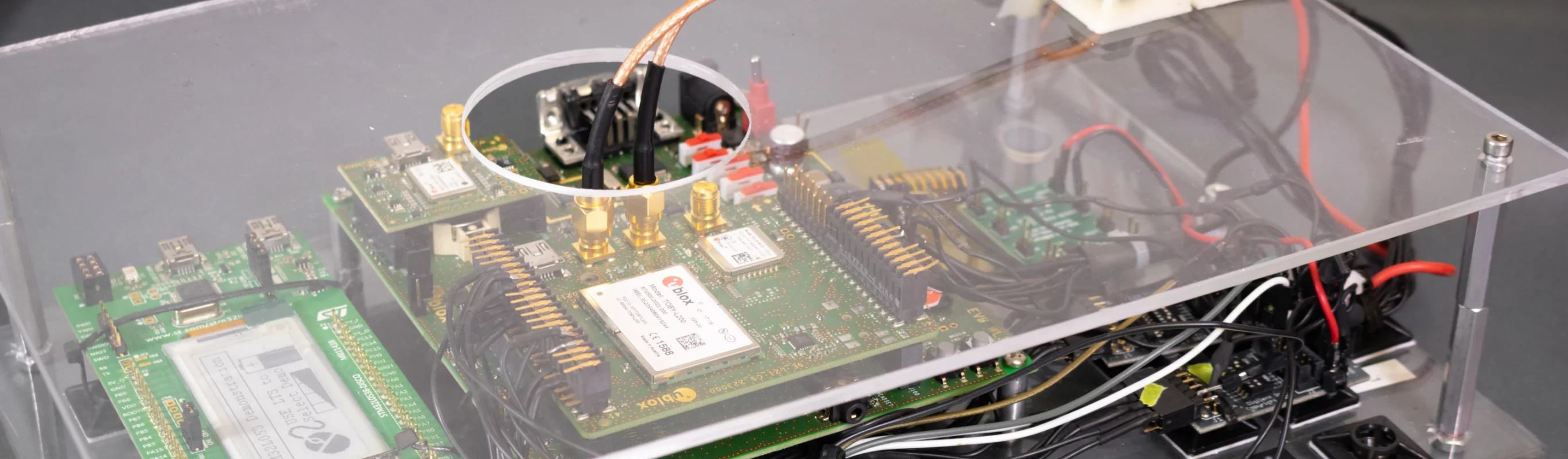
7. Manufacturing Support
We do more than just design
With more than ten years in the business, we've developed manufacturing relationships in the GTA, Ontario, and Asia. We can help you find the right manufacturing option for anything you need—metal, plastic moulding, PCB, PCB assembly, component distribution, packaging, boxes, printing, even fabric.
Our ‘above and beyond’:
•        We can help you plan out and ramp up your production, from small test batches to high-volume runs
•        Use our test jigs to verify your components before they go into assembly
•        We can deliver to you an assembled and tested product, ready to ship.
8. Deployment & End Customer Support
Peace of mind for your customers too
We look for opportunities to supplement and augment our clients' existing team to deliver superior products. We want our customers to feel like we are their own in-house engineers. We want to provide piece of mind to your customers too.
Our services:
•        White label support as part of your team to help in-house technicians and engineers deploy the unit
•        Our engineers are on hand to address any issues that crop up which we haven't encountered in laboratory testing
•        We support you with any upgrades or technical support you need with your final product