We love working on IoT connected devices. Do you have a great idea in mind that you would like realized? Contact us today to know how we can help.
Electronic Component Shortages and its impact on Product Design and Development
Having been in the industry for over two decades now, I have had the opportunity to witness quite a few fluctuations in the global Electronic industry sector. The Electronics Industry market is cyclical in nature with demand influencing the state of the components market. We have seen periods when component representatives don’t answer our calls or respond to our emails because of the lack of available components and there have been times when they come to meet us every other day because of excess components available, enticing us with great offers and discounts.
But none of the previous downturns have been as severe or long-drawn-out as what we are experiencing today.
In this blog I attempt to provide some context into the current components shortage issue by focusing on trends, the reason for demand and shortage and the impact on product design.
2000-2020 (Setting the stage)
Following almost two decades of continuous growth and prosperity (1980 to 2000), the turn of the century witnessed a combination of several downturns. The Dot.com burst, 9/11 attacks, Sub-Prime Housing Crisis and the great recession. So how was the electronics component market affected?
In 2001, because of the electronics industry downturn, the technology market sagged unexpectedly, leaving manufacturers and suppliers with huge amounts of unwanted inventory valued at billions of dollars. Reportedly, component makers, distributors and customers wrote off around $13 billion worth of semiconductors that either ended up in the gray market or were sold to brokers for small fractions of their initial value.
Despite this situation, from 2000 to 2020, chip manufacturing capacity expanded steadily by around 4 percent annually, keeping up with sales. In parallel, semiconductor utilization has also been consistently high (at or above 80 percent) over the last decade, with 90 percent utilization in 2020. Therefore, while the semiconductor industry has increased its production capacity by nearly 180% since 2000, its total capacity was nearly exhausted at the 2020 level of utilization rate.
Because of the 2001 lesson, for the last two decades, the electronics supply chain has been focusing on efforts to minimize inventory in its pipeline via just-in-time (JIT), Lean and build-to-order (BTO) strategies. The goal was to deliver only the required number of components to manufacturing lines.
But historically, forecasting in the electronics industry is known to be notoriously inaccurate. So, minimizing inventory will not always pay off. No one was prepared for the surge in electronics in 2020 and for what followed.
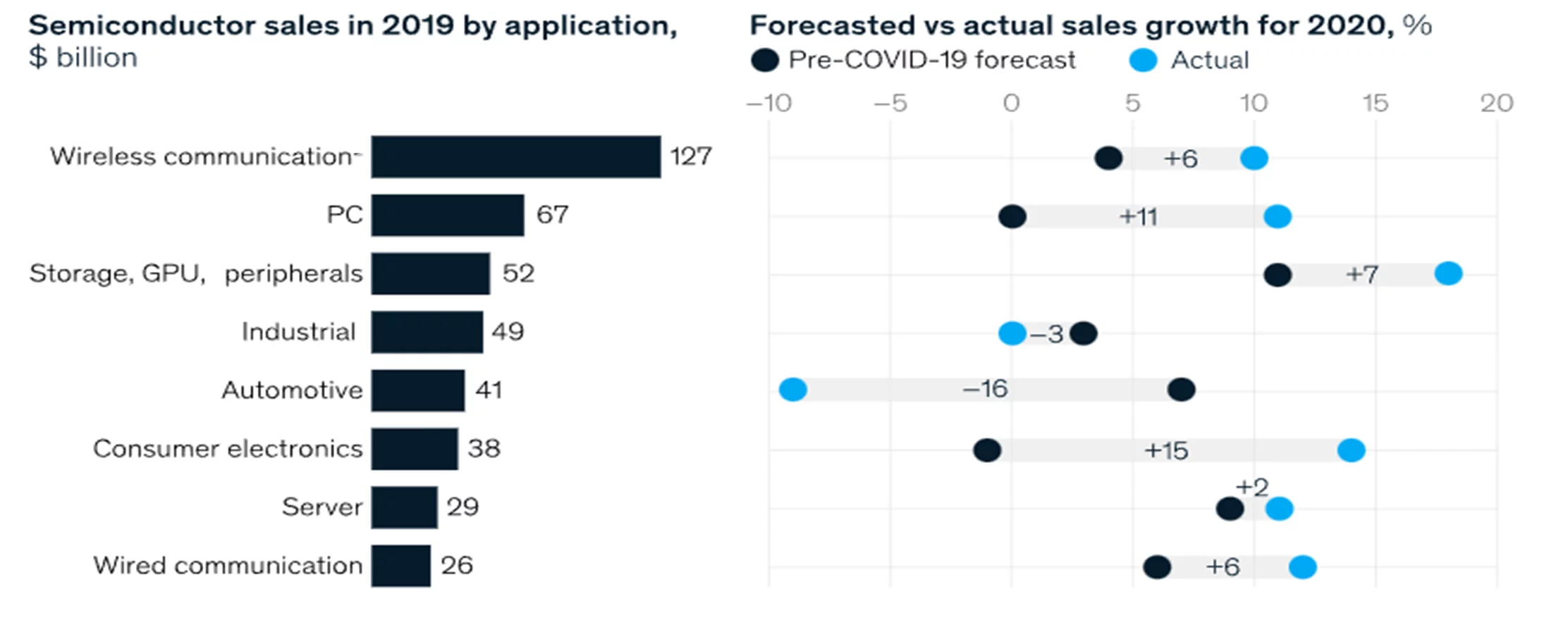
Fig1: Forecasted vs. actual sales growth of semiconductor sales in 2020 across applications (Source: McKinsey Report 2021)
The graphical representation (Fig1) explains how forecast did not match actual sales in 2020. With the exception of industrial and automotive applications, all other applications saw the actual sales rate grow much higher than the forecasted rate.
All these factors set the stage for what was to follow in 2020.
Why the demand?
Let’s look at a couple of factors that resulted in this increased demand in the recent years:
Emerging IoT and IIoT market
IoT and IIoT has been gaining ground over the last couple of years. Today, you can find a sensor in nearly every device around us. Factors that contribute to the rise in adoption of Internet of Things include high penetration of Wi-Fi connectivity and internet, technological enhancements in wireless network technologies, increased adoption of cloud platforms and development of smart industries like smart cities, smart transportation, smart agriculture and more.
Rollout of the 5G technology
Initially rolled out in 2019, 5G networks are estimated to cover one-third of the world’s population by 2025. The 5G network impact on current and future applications is driving increased demand for electronic components. 5G technology is more complex and will demand more components.
High adoption of smart electronics
With higher disposable incomes, there is increased adoption of smart electronics that gets updated every couple of years. As witnessed by the huge demand, popularity and enormous power of the Apple brand name, even incremental, modest upgrades warrant a new smartphone generation launch that are always hugely successful. Users yearn to stay updated on latest technology by upgrading their electronics every few years. Earlier the average lifespan of consumer electronics was around 40+ years and over the years it has dwindled down to an average of 4-5 years. This trend has resulted in an increased demand for components to whet the appetite for trendy, smart electronics.
EV & Modernization of automobile cockpits
Electronic vehicle adoption is picking pace globally for the benefits they provide, but they need a lot more electronic components to support its functioning.
Automobile cockpits of all vehicles today are highly modernized offering a wide range of features that require modern, powerful, components.
Self-advancing cars are another category on the rise that requires powerful electronic components on board to support complex infotainment and navigation systems.
An interesting trend that emerged during the pandemic was the demand for personal transportation vehicles like electrical scooters, e-skateboards and segways.
Lifestyle Changes
During the pandemic, the world moved largely to working from home and at-home schooling which led to an increased demand for communication infrastructure, from laptops to cameras, Wi-Fi Access Points, routers, switches, etc.
Another trend that emerged was the demand for at-home exercising equipment. Interestingly, Peloton shares grew over five times from mid 2019 to the end of 2020.
Why the shortage?
It was not just minimized inventory practices or inaccurate forecasting that led us to this stage. There were several factors which together compounded the effect by a large degree and so I like to name this part “The death of 1000 cuts”.
Pandemic shutdowns
The pandemic resulted in entire cities shutting down across the world and while this affected economies globally, having most of the chip manufacturing based in the Far East, was a serious blow to components supply.
Global supply chain
The Covid-19 pandemic exposed a weak link in the global supply chain. Only Taiwan’s TSMC, South Korea’s Samsung, UMC and SMIC are responsible for most of the world’s chip manufacturing. These dominant players produce most of the leading-edge chips used in mobile devices or for military applications.
The trade wars tension between US and China and the sanctions imposed on Chinese foundries have also led to additional stress on Taiwan and South Korean foundries’ capacities.
Automotive Industry
At the beginning of 2020, the automotive industry came to a grinding halt due to the inaccessibility of components and the business model of “just in time inventory” that ensured no excess component stock. Moreover, demand for automobiles also saw a sharp decline as most people began working from home.
By the end of summer 2020, demand for automotives rose again with an interesting new segment: scooters and e-bikes.
Natural Disasters
On October 21, 2020, a fire broke out at Asahi Kasei Microsystems (AKM) at their Nobuoka semiconductor Plant “Fab2”. This factory mainly produces large-scale integrated circuits (LSI) used in audio equipment, home appliances, TCXO oscillator, and other products. The fire took four days to extinguish but the factory was left severely damaged and shut down production lines. The factory was scheduled to reopen in March 2022 and has reportedly resumed production as of today.
From March to June 2021, Taiwan suffered the worst drought the country has seen in 50 years which left TSMC and other manufacturers struggling to attain the necessary quantities of water, a crucial element in chip manufacturing.
In mid Feb-March 2021, a deep freeze in Texas (Winter storm Uri) caused numerous chemical plants to shut down as the whole state lost power, disrupting a global supply chain for resin operations and polyethylene causing a significant plastic shortage.
In March 2021, Japan's Renesas Electronics halted production at one of its main plants in Hitachinaka, northeast of Tokyo, after a fire broke out. The fire, caused by an electrical fault, was a blow to carmakers around the world already as Renesas is supplying about 1/3 of the automotive chips.
In March 2022, a 7.4 magnitude earthquake struck off Japan’s northeast coast of Fukushima Prefecture (March 2022) halting production at several semiconductor plants including Renesas, Fujitsu, Murata and Kioxia.
Man-made Disasters
In 2021, the Suez Canal blockade also contributed to the global chip crunch. The blockade of the world’s busiest and crucial shipping waterways occurred when a container ship got wedged in the canal causing a logjam of hundreds of other cargo ships.
The current Ukraine conflict that escalated in 2022 has also impacted global chip supply. Ukraine is home to two leading suppliers of semiconductor-grade neon, critical for the lasers used to make chips. These suppliers who produce about half the world's supply of neon, have halted their operations, threatening to raise prices and aggravate the semiconductor shortage.
Cyber-attacks
Cyber-attacks on logistic companies, is another reason for the supply chain disruption seen in recent years. Cyber-attacks are not new and have been known to occur every few years in the Transportation & Logistic sector. But now, there seems to be one or two each month, with some being very prominent. For example, a cyber-attack in May 2021 effectively shut down the Colonial Pipeline, which provides gasoline to almost half of the east coast of the United States, for about a week. The company said that the cost of the ransom and the disruption to business could run upwards of $50 million.
Shipping Logistics
A chain is only as strong as its weakest link which holds true also for supply chains.
Even before the pandemic, the world started seeing some worrying signs that impacted global supply chains. Trade tensions between US and China, escalated under President Trump with the introduction of unprecedented tariffs and sanctions. This created volatility in supply and demand as companies on both sides of the globe rushed to stock inventories ahead of the implementation of tariffs. The unexpected shift in trade put the initial stress on global logistics.
During the first half of 2020, demand for most goods went down as economies worldwide went into lockdown and there was much uncertainty on what is to come. But in the summer of 2020, thanks to massive fiscal stimulus, imports to North America surged and consumers flooded online retailers with new orders.
By late 2020, real cracks in the supply chain started to emerge. From a logistics perspective, restarting the global manufacturing machine after the lockdown turned out to be quite difficult. There was a severe shortage of shipping containers at the time as several containers were being used to ship PPEs and other supplies to South America. Unfortunately, most containers were left at site, disrupting an already weak logistics system. Add to it, the shipping rates for certain routes skyrocketed, congestion developed at international ports that then spread to railroads and inland rail terminals, exasperating the trucking and chassis shortage. At one point, we heard that containers at ports in Vancouver and Los Angeles were being held for months to be unloaded.
All this led to a point where container prices were soaring up by around four times its normal value, adding more stress to an already weak system.
What is our current state?
All the above stated reasons compounded the affect on global component shortages. Let’s look at where we stand now and what the current scenario seems like.
Allocation Mode
Most chip manufacturers have now resorted to assigning allotments to their customers regardless of demand to try to balance the situation. Allocation is though seen as a band-aid solution for when demand for components exceed manufacturing capacity. Without sufficient components from manufacturers, suppliers are forced to allocate partial quantities and schedule deliveries over a period of time. Leading component manufacturers are asking for forecasted usage and advance Purchase Orders projected till the end of 2023. As of now, the average waiting time is in order of 52 weeks or even higher.
Danger of fake/ knockoff chips
There is a possibility that unscrupulous characters under undue pressure from customers to fulfill orders by any means necessary, may resort to accepting fake/knock-off components. These parts are readily available on online marketplaces and seem convincing enough. There are some parts that are imitations, some that are worn-out or broken parts repaired to appear new, and then there are completely different components that are rebadged.
Components cost
As demand is currently higher than supply, component prices are soaring like never before. We have experienced situations where components were charged six to ten times higher than their ‘regular’ price. Manufacturers with deeper pockets can afford to pay a premium to ensure their lead times are maintained, but this is not the case for everyone. The inflated price that is being paid for the components may ultimately have to spill over to the end user which is already being experienced and reported.
Investments, Expansion and Acquisitions
TSMC has announced that it plans to invest $100 billion over the next three years to increase its capacity to meet rising demand.
Intel has announced that it plans to spend $20 billion on expanding its fabs in Arizona, opening its doors to produce chips for other companies, thereby adding a new major supplier to the marketplace.
Four new factories (two by Intel Corp and one by TSMC in Arizona, and another by Samsung in Texas) are slated. China too has offered a myriad of subsidies to the chip industry as it tries to reduce its dependence on Western technology.
In Feb 2022, Intel Corp announced that it is buying Israeli chipmaker Tower Semiconductor for $5.4 billion, giving it access to more specialized production, to take advantage of soaring semiconductor demand.
New Technologies Introduction
Advancing technology now calls for newer 1, 3, 5 and 7nm components while the dominant request for components is still for older technology like the 190nm chips.
This is the reality of today.
Impact of Chip Shortage on Design Industry
This section of the blog will analyze some interesting data that was put together in a report titled “Deconstructing the Chip Shortage” published by our partner Avnet in March 2022.
The survey was conducted among more than 500 global engineers: 31% of respondents were based in the Americas, 56% in EMEA, 10% in Asia and 2% in Japan. The respondents represent a wide range of companies from contract manufacturers to electric vehicle makers.
When the respondents were asked on how they dealt with component shortages, this is what they had to say:
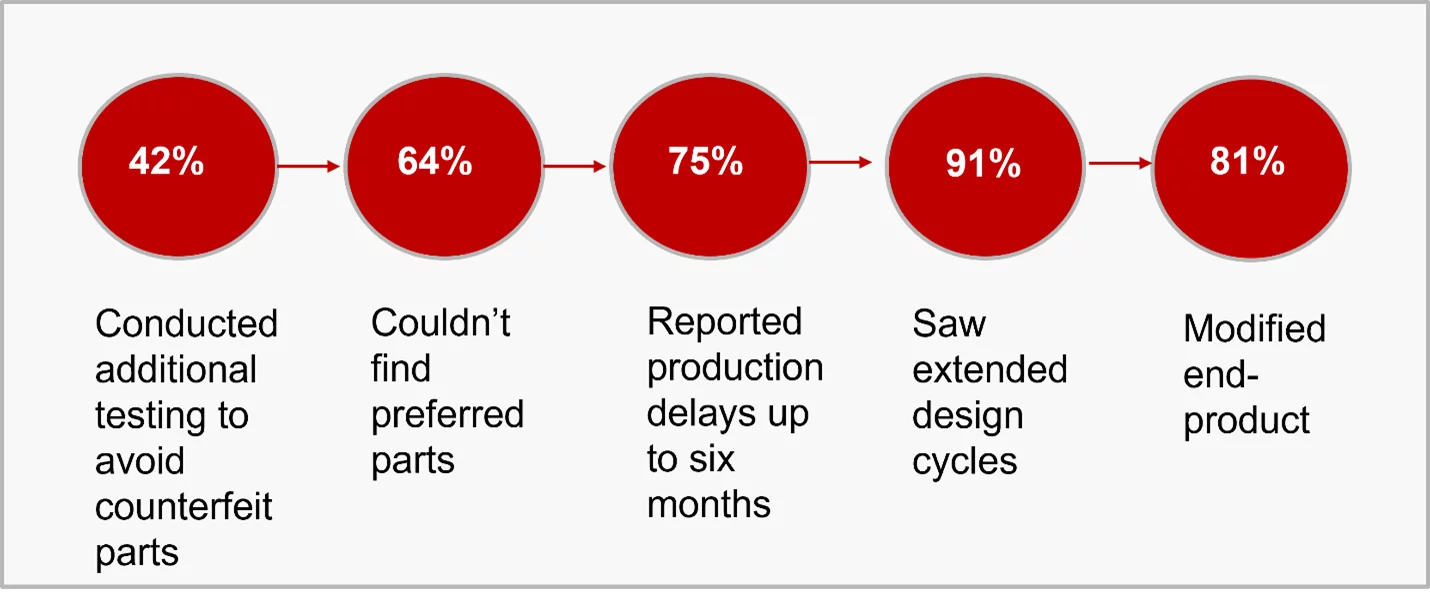
Fig2: Chip shortage impact on Engineers (Data source: Avnet Insights March 2022)
In terms of production delays, half the respondents said they are experiencing a production delay of around 3-6 months currently.
The category the respondents were most concerned about was the availability of MCUs. Today MCUs can be found in just about every type of electronic product. The challenge with MCUs is that unless a drop-in replacement is available, changes are required not only for the hardware but also for firmware. In many cases, these modifications may be extensive enough that a redesign is likely to be easier and quicker. Today lead times for many MCUs have stretched to 50-52 weeks and more. In terms of pricing, MCUs have seen the biggest mark-up of all component types, with some reporting increases of more than 10 and even up to 20 times the pre-pandemic pricing.
The survey also shows that engineers don’t expect the situation to change much over the next 12-18 months. In fact, a strong majority expect lead times to worsen and prices to rise in the next 18 months.
What can we do?
In this section, we address some action points that can be implemented to address challenges of the times.
Design for disruption (DfD)
Product redesign becomes a very effective way to create alternatives to critical parts that might become hard to procure; DfD allows companies to maintain a product’s function while using different materials or components.
This holds true in the case of New Product Development and for product update/maintenance where a product is updated with new technology while replacing legacy technology.
Ecosystem innovation
It is important to foster closer collaboration with suppliers, partners and customers, which in turn requires closer and more transparent communication, so that every player can factor in the full set of information and uncertainty, and plan more effectively for the long run.
Advance Planning and Purchasing
Work with your design firm to understand the components required for both prototyping and the various stages of production. Design houses usually have longstanding partnerships with key component manufacturers, vendors and distributors and can help to quickly identify and source the right components needed to meet the project goals.
As soon as the product design is finalized, tested and validated, place purchase orders for mass production. Even if it will be a couple of months before production at scale starts, it will be smart to have the necessary stock in place. So, get on the allocation list as soon as possible.
Drop-in replacements
Ask your design house to look for alternate options for components that are not too critical. Having a list of vendors that offer drop-in replacements prepared in advance, can help reduce the risk of component shortage while moving into production.
These are some of the ways to mitigate components shortage through design engineering. The general consensus among leading chipmakers is that the global chip shortage will continue into late 2023, though most bottlenecks should ease up by end of this year. I came across a very insightful 2022 report from Gartner that showcased the semiconductor inventory trend over the last two decades and it was very interesting to see the cyclical nature of inventory index in its graphical representation. It was very positive to see the position as it stands now which is under ‘moderate shortage’ with forecast of the index moving towards normalcy very soon. There is much to be done to improve inventory practices and I believe we now know better. Let’s hope the supply-demand deficit is corrected sooner, than later.
At NeuronicWorks, we assist with component obsolescence management by finding and validating the required components or by modifying or redesigning PCB modules in part or in its entirety. Contact us today to know how we can help.