Are you looking for prototyping or manufacturing services to scale your product to market? Look no further, contact our team today to see how we can help.
Jet Printing in SMT Assembly
Jet printing has today matured into a powerful technique for high accuracy, high flexibility, and increased production efficiency. Jet Printing is a technique that is vastly different from the traditional solder paste deposition method. It allows for a high degree of flexibility in PCB Assembly prototype production, making it not only easy but also quick to adapt as new revisions are needed. This process allows control of solder paste deposits with increased accuracy and precision. With an increased level of control, jet printing allows to meet tight tolerances, complex patterns, and reduced size.
Jet printing is a non-contact printing process that deposits solder paste in pre-programmed locations on a board at high-speed by a unique ejection method eliminating the need for stencil tooling. In high-reliability industries like medical, automotive, and aerospace, it is extremely crucial to have exact solder paste deposits not just in quantity but even in geometry as every deposit will be controlled, measured, tracked, and traced with this new technology.
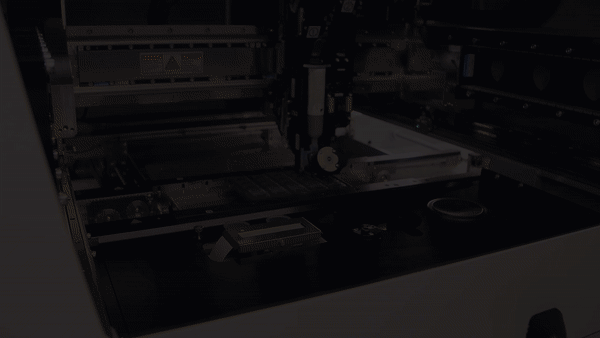
Figure: Jet printing in process
The traditional type of solder paste printing is via stencil printing. In this method, stencils, which are laser cut sheets of steel, are used to imprint solder paste onto PCBs. The stencils are customized specifically for a PCBA, and holes are created via lasers to position and place surface mounted components onto the PCB.
There are various stencil types like laser-cut, laser-cut nano coated, stepped, and E-formed stencils. While laser-cut stencils are common, a recent market innovation has the option of nano-coating the laser-cut stencils to improve paste release by smoothening aperture walls. Nano coated stencils are expected to perform almost like E-formed stencils but will cost lesser.
E-formed stencils are more expensive and offer improved solder paste release and print performance for micro BGA component or any type of component down to .55 (mil).
Stepped stencils are used to achieve different solder paste heights and are a popular method of increasing or decreasing solder deposit on selective areas to deposit less paste (stepped down) for small components or increased solder (stepped-up) for connectors or components with bigger pads.
Why Jet Printing?
With stencil printing, one of the biggest challenges is that any minor change to the PCB layout design, will require a new stencil to be created and used, thus driving up costs and resulting in delays. Jet printing on the other hand is the more economical and efficient method allowing instant board revisions and changeovers.
Due to its obvious merits the technology can be used alone to support the paste application process for a PCB Assembly production on its own. Additionally, jet printing can make the paste printing process more robust, a jet printer can be added after stencil printer to avoid the use of expensive stepped or e-formed stencils.
Although Jet printing takes longer to print, it gives Zero NRE (non-recurrent engineering) cost and more process control. The lead times and costs associated with sourcing, managing, and storing stencils is saved when opting for Jet printing. Both Stencil printers & Jet printing machines can check the presence of solder paste though only the jet printer can identify and repair any less coverage areas to at least minimize or eliminate the defect related to solder paste deposit.
Moreover, it takes only in 5-10 mins using ODB++ or less than 30 mins using Gerber file and XY coordinates to create the program for a jet printer.
Some of the additional benefits of Jet Printing include:
1. Ability to apply glue and solder paste in the same process using dual heads
2. No stencil requirement
3. Purely Software driven which make process line optimized
4. No stencil storage required
5. Eco-driven with lesser wastage, saving costs as almost all the paste in the cartridge will be used.
6. Capable of solder paste presence inspection and repairing any missing paste at the same time
Jet Printing: Cheat Sheet
Here are two important points to keep in mind for successful Jet printing:
1. Always set the correct volume setting as per pad sizes
2. Know the solder paste performance as per volume settings
Here are some important settings that eliminate solder defects such as solder balls under discrete components, bridging, and insufficient and excess solder. In our process at NeuronicWorks, we currently use Type 5 solder paste and AG Ejector:
- volume setting 100% for base point and 52% for the center point
- volume setting 80 for minimum pad size 1-2mm x .6mm -.33mm
- Volume setting 35-50 for pad size .33mm x .33mm
- use the volume setting 50-60 for pads size equal or lower than 1mm x .33mm
- Reduce thermal pads size under the component by 20% and set volume to 50
- volume setting 80 for minimum pad size 1-2mm x .6mm -.33mm
- Volume setting 35-50 for pad size .33mm x .33mm
- use the volume setting 50-60 for pads size equal or lower than 1mm x .33mm
- Reduce thermal pads size under the component by 20% and set volume to 50
- volume setting 65-75 for minimum pad size 1-2mm x .33mm
- volume setting 100 for minimum pad size equal or bigger than 1.5mm x .575mm
- Volume setting 43-67 for component pad size .33mm-.5mm diameter
- Volume setting 70-80 for component pad size bigger than .6mm diameter
- Volume setting 80-100 depending on the height and width of the component termination
- Thermal pads under the component should be reduce to 20% and volume setting 50-70
- Volume setting 100 for connectors and Switches without fine pitch
- Enter the PCB thickness and Hole diameter, Lead dimensions as cubical length .5 and width .5- and Single-hole deposits with volume setting 100
- SMT pads volume setting 80-100 depending on the board thickness
1. Discrete components
   - Use Center Point Strategy, Rank 69%
2. LGA components
    - Use Standard Strategy, Rank 60%
3. QFN, DFN and other Lead less components
   - Use Standard Strategy, Rank 60%
4. QFP and SOIC Components
   - Use Standard Strategy, Rank 60%
5. BGA components
    - Use Standard Strategy, Rank 60%
6. D-Pak and inductor components - Use Standard Strategy, Rank 60%
7. Connectors and Switches - Use Standard Strategy, Rank 60%
8. Connectors with SMT Pin with Pin through-hole - Use Standard Strategy, Rank 60% and use Pin In paste
9. For noncomplex design:
    - Volume setting 80 is assumed to be equivalent to 5 mil stencil thickness
    - Volume setting 70 is assumed to be equivalent to 4 mil stencil thickness
Based on our experience, each solder has different setting on volumes and performance in the process. However, jet printing provides accurate and speedy results, shortening delivery times and enhancing responsiveness that lets us act quickly when necessary.
At NeuronicWorks, we focus on prototyping and high-mix, low volume manufacturing and use Jet printing for its flexibility and accuracy. With ODB++ we can have the program for paste printing ready in 5-10 mins, depending on the complexity of the PCB design. We optimized our line process to run a product in less than 5 days, once all components are in hand.