Keep in mind that accredited test labs are not legally allowed to provide consulting services for certification and regulatory compliance. However, NeuronicWorks can help you along and make sure that your product will be certified to the industries where it is used, geography where it will be sold and to market it without any foreseeable delays, which can occur for the above-mentioned factors. With our experience, we can ensure that none of these factors will result in a delay in getting your product-to-market.
Preparing for Certification: Product Development
Taking your idea in the form of a product to market involves a series of detailed steps and processes: product and concept definition, requirements generation, detailed design and engineering, reviews, prototype production, pre-certification, final equipment certification/regulatory compliance before manufacturing and distribution.
This process is extensive and involves multi-disciplinary engineering design considerations that must be taken into account at every step of the NPI process for a successful entry into target markets in different countries. Remember that even the smallest oversight can send you back to the drawing board resulting in additional costs and setting you back a few months, and so it is critical to work closely with experts who can guide you through the whole process cautiously and meticulously. We at NeuronicWorks have a great team of experts who can guide and support with the certification process at any point during the design journey.
This article from our Senior Systems Compliance Engineer, Robert Legault, provides some insight into how you can prepare for the certification process from a design perspective to ensure success while saving costs and time. Read on to understand the key pointers that can help you through the entire lifespan of the product: design, pre-certification, and post-certification.
Preparing for Certification: Design Phase
- At the onset, it is critical to list and determine several factors that will steer the direction of the design phase. This includes: Geography and Industries
- Determine the geographic markets where the product will be sold. Each Geographic region will have a different set of standards that will apply, and it is critical to be aware of this early in the design stage.
- Also determine which industry the products will be sold (i.e., agriculture, automotive, industrial control / measurement / in vitro diagnostics for laboratory (or home use), mining, medical (home or professional setting), etc.), if the end products will be without software or firmware, will it be an IT video/audio product for professional or consumer use. All these equipment types have different standards of requirement or certification for both safety and EMI/EMC compliance for both non-wireless and single/multiple wireless radio equipment.
- If you are not certain, always start with the North American (US/Canada) market for certification process.
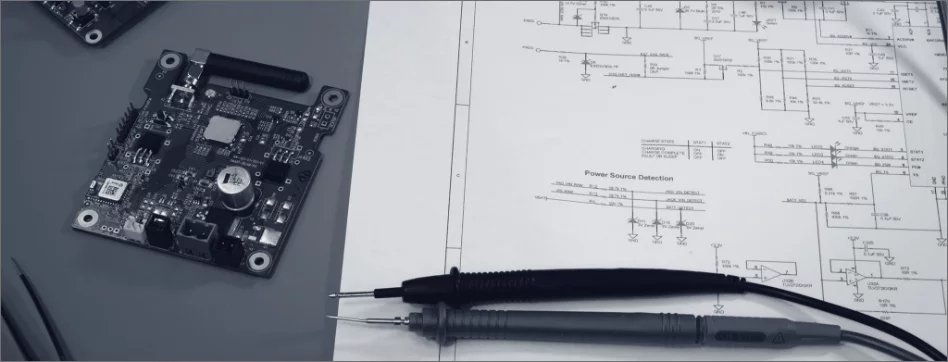
- Component Selection:
- Evaluate the components to the end product’s safety reference standards for the geographic regions where the system is to be sold and put into market.
- Make sure that the safety and wireless critical components have appropriate markings for the markets where the product is intended to be sold. If its outside of North America, then it needs the CE mark for EU and its economic partners, if it’s going to be sold in South Korea, Taiwan, Japan, China, the EAC necessary emission and safety markings are required.
- When it comes to Europe, always consider that equipment bearing the CE mark will require compliance to the Low Voltage Directive, the EMC Directive, the RED (Radio Equipment) Directive (wireless radio product only), the latest RoHS directive, WEEE Directive, (disposal of electronic equipment directive), and the latest published REACH (substances of high concern) regulation. One can review and test non-certified/recognized component(s) to the applicable component standard (as listed in the system standard), or in some cases, per the system safety standard. The system safety standard will refer to other standards that are required for the individual critical components.
- We advise to review the applicable EN, UL and CSA system standards for the equipment, and the UL or CSA standards for the individual components/sub-assemblies. Keep in mind that the US and Canadian overall product Safety standards are mostly bi-national harmonized type and are typically adopted from the IEC international standards. These standards will give you an idea about the component standards required for certification. At NeuronicWorks, we ensure the use of NRTL/C and/or IEC certified components, based on the geographic region where the product will be put on market.
- To legally apply CE marking, compliance to the ROHS III Directive (EU 2015/863 March 2015) is mandatory in Europe; the similar California 65 proposition requirements on restriction of hazardous substances is legal requirement if you want to sell in that state. We strongly urge you to always use RoHS 2 or RoHS 3 compliant parts including polymeric enclosures, electrical components, wiring, PCB Assembly components, bare PCB and insulating materials. If not certain, the information can be found from the marking on the product. If that’s not available, look at the datasheet / Spec sheet or contact the manufacturer to get the required information. They can usually supply a certificate or a declaration of conformance or they may even share an entire materials test certificate and report.
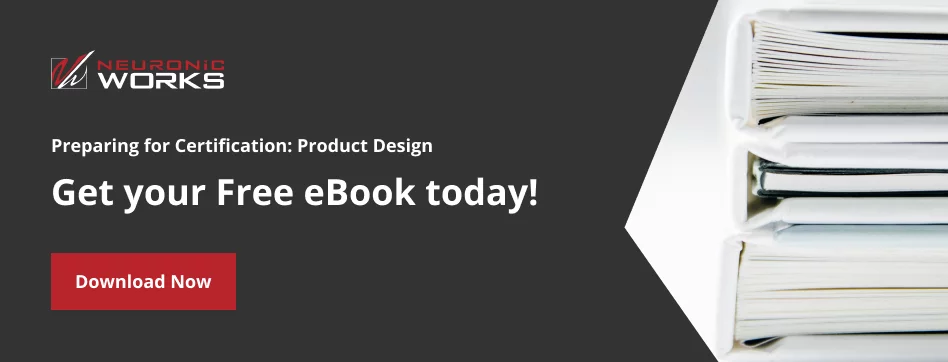
- Safety Critical Component / Product Certification Status:
- You can use online certification status databases from accredited safety agencies (UL, CSA, Nemko, TUV SUD, TUV Rheinland, Intertek and others) to search for accurate certification approval listings. For example, the UL Product iQ certification status database lists the components and assemblies that are UL recognized to the applicable UL and / or Canadian safety standard(s).
- Never assume that the product certification comes from a particular certification agency (UL or CSA); make sure to review multiple authorized certification agencies websites per above. When the certification file is found, it is important to get the test certificate from the accredited laboratory, so it can be given to the respective safety laboratory engineers as proof of regulatory compliance. What’s listed in a datasheet is typically not sufficient, especially when dealing with critical safety components such as power supplies.
- Use components according to datasheet specifications with suitable derating based on the highest expected ambient temperature that the component will experience, per your design specification and/or sales literature.
- Check for conditions of acceptability. Make sure to carefully review the rating of the product over a period, maybe look at an alternative in the same family with a higher rating in terms of power, current and voltage.
- Double check that certifications/approvals are current and updated. While reviewing an older datasheet, it is possible that the manufacturer has obsoleted or discontinued the product and delisted the certification. Always check for the latest datasheet and if possible, research on the latest certification database to make sure that its still certified to the same standard as the previous version. Many times, for instance with safety critical components, if there is a UL standard, there is a UL EXXXXX file number which you can find on the UL Product iQ database to make sure that UL approval is still valid. If you are not certain or you cannot find anything relevant, the next best thing to do is to start by checking if they are selling it in Europe, look for an EU declaration of conformity, which is a publicly available file on the internet. If that is available, then there will typically be a version of the application standard or regulation in North America as well. It is a good place to start and if in doubt, one can always contact the manufacturer and get the certification reports for both safety and EMC/EMI compliance to present to the certification agency safety engineer at the accredited laboratory.
- Design Suitable Enclosures:
- To design a suitable metal alloy or polymer plastic enclosure, there are certain requirements that must be adhered to in the system safety standard such as material selection, thickness, thermal control/ventilation openings, rigidity, enclosure tests, robustness, and suitability for applicable environments. For instance, in the case of a portable or movable product, a drop test could be involved, there may also be an impact test, or a rigidity test provided for the product. In the case of polymeric plastic materials, obtaining an UL 94V-0 rated product certification from the enclosure manufacturer is essential. It is critical to provide test certificates or equivalent documents showing flammability rating to the safety engineers.
- Determine Required Spacings (creepage and clearance):
- Identify the circuits via physical layout or wiring diagrams on the final product and the insulation rating of various critical safety components (terminals, relays, fuse holders, overvoltage protection circuits, wiring, terminals, etc.) and determine how close they are to other circuits, components and to the enclosure parts and other non-live mechanical parts. There are clearance (over the air) distance requirement tables (based on highest voltage present, & pollution degree) in the UL/CSA/EN system safety standard. If the distances measured are not per the applicable table, you can always use additional safeguard (basic - specific instructions, labels) and supplementary or reinforced insulation parts/materials with suitable flammability rating per UL 94 standard. Use of these additional safeguards will required review/inspection and/or additional testing per the system standard by safety engineers to show compliance.
This practice also extends to bare PCBs- one needs to be aware that bare PCBs both on the surface layers and in the internal layers require certain creepage requirements that are necessary and that are typically in the system safety standard; all PCBs must be UL recognized. One should be aware of clearances over air to off-board components (of different voltage) and creepage over surface between components. There are many ways to achieve this: In the case of creepage, if the distance is under the minimum requirement for that pollution degree on the PCB, including additional insulation and/or the use of proper routing on the PCB to increase the creepage distance is one method. Remember that clearance is always measured over air between circuits or components of different applied voltage and grounded or electrically neutral components.
- Prepare for single fault and abnormal operation tests:
- Single Fault and abnormal operation tests are required per the latest UL and CSA product safety standards based on the IEC safety standard and must be tested by the safety engineer at the accredited laboratory. The equipment should withstand application of a single fault condition (i.e., safeguard failure, or short-circuit/open circuit of critical ICs or safety components) or application of an abnormal operating condition and remain safe. Temperature tests for critical components and enclosure will also be applied. Different components have a different maximum temperature rating. Note that if your literature (i.e., your product user manual) states that the equipment will function beyond the normal ambient of the laboratory (i.e., 25° C) to say 50° C that temperature (i.e., 50° C) will then be added to whatever rise of temperature the lab measures for temp testing. If it is very close to or exceeds the temperature rating of the component system or enclosure, it will then be considered a failure and additional means will need to be implemented to correct it. This may involve higher forced air cooling, higher temp. rated components, or require that you lower the maximum ambient temperature rating in your literature or possibly a re-design effort.
Pre-certification support
Precertification can help mitigate risks of late penalties and redesign costs, to avoid unexpected challenges at the last minute, by testing as early s possible in the design cycle. NeuronicWorks helps with pre-certification support, working closely with our customers to minimize the risk of test failures and re-assessment during certification, helping you finish your projects in time.
- There may be additional features to the product which will have to be verified for compliance to the required Safety and EMC/EMI standard and/or FCC regulation. This includes routing of wire harnesses, and location of PCBA modules and power supply within the enclosure. Always make sure not to mix low speed-low voltage analog with high-speed digital RF cables. If using shielded cables, then ensure they are shielded from end to end and fully 360 deg. bonded to the connectors, or at least to one end depending on the requirements of the design. For internal system cables that are unshielded, make sure they are as short as possible and are not routed over radiating components or sub-assemblies that may couple to the wires. NeuronicWorks Inc. can perform a safety and EMC/EMI compliance review on the product prior to any pre- or full certification by an accredited laboratory.
- For pre-certification testing, NeuronicWorks Inc. will take the initial prototype boards or products to an accredited ISO 17025:2017 laboratory for EMC radiated emissions scan to applicable FCC regulations, ISED (formerly Industry Canada) standards and/or EN 550xx standards. With RF circuits, fast analog and fast digital circuits, there will always be emissions coming out of the product even with proper shielding. It is a good idea to take this to an accredited lab so that they can do a scan to the applicable standards / FCC regulations that will apply to the product. Depending on what is required and depending on the highest frequency of the circuit, including the wireless radio transceivers, this may go up to several dozens of Gigahertz. Note that there are different limits for different classifications of products according to both the EMC directive in Europe and the FCC Part 15 or Part 18 and ISED ICES-00x EMC and RSS-2xx wireless radio compliance standards. For example, if it is a commercial, hospitality or industrial application, then it is called Class A. If it is a home application, then it is Class B. Class A level conducted and radiated emission limits are typically higher than Class B. If you think the product will be used in a home/residential application, ensure emission levels are below Class B limits.
Full certification
The applicant will bring the system product to the accredited laboratory for inspection, review and testing to the applicable standards. The applicant must provide all the documents, certifications, as well as special test firmware, PCB assemblies, bare PCBs, schematics critical parts, Bills of Materials, instruction manuals, labels etc. For our designs, NeuronicWorks will fully support you with all this material and ensure a seamless process.
- The laboratory safety engineer will review all materials, perform necessary inspections and testing, then create a proper CB (International) or NRTL/C (US/Canada only) test report to the applicable safety standards. Another engineer will review all materials, wireless module certifications, and create and EMC/EMI test report & test certificate related to the applicable EMC emissions and/or EMI immunity susceptibility standards and/or FCC regulations. Be aware that the system/product installation guides and/ instruction manuals, have requirements in the system standard for warnings, cautions, and other safety related information that typically may or may not be present on the labels of the product depending on its size. It is recommended to consult with NeuronicWorks Inc. certification group ahead of time to determine what is required for the system standard. NOTE: Label materials and suppliers must be UL recognized and CSA certified; alternatively, labels must be printed from a UL recognized/CSA certified label printing system.
Post certification support
Post the certification of a product, there are multiple considerations to keep in mind in terms of manufacturing, testing, components obsolescence and literature (i.e., instruction manuals, user guides etc.). NeuronicWorks provides complete post-certification support and ensures product success in the market.
- Validation test for manufacturing – Make sure the equipment being produced meets the functional requirements or specifications of the customer base and will be available for large volume production with hopefully little or no rejects using the same components and layout design submitted to the safety agency for certification.
- Production Dielectric (Hi-Pot) and Earth Ground leakage (medical devices) testing – Depending on the nature of the product, if there are power supplies involved, there will be a need for ground testing for production and dielectric hi-pot testing.
- NeuronicWorks Inc. also provides component obsolescence and long lead time component replacement management support. We look at what is on hand and if there is an issue with an obsolete component which becomes apparent soon after post certification, we help find a suitable fit form functional product. In the case of critical products, you may have to go back to the lab and request a review. We suggest you provide as much certification information, test reports and certifications you can to the safety engineers so that they can double check to see if it meets the requirement of the original CB or NRTL/C safety test report and the design and the environment where it will be used.
- NeuronicWorks Inc. has a strong network of supplier partners that ascertain the critical components being used is still certified to the standards required in the CB or NRTL/C safety test report for the product. As mentioned earlier, sometimes the component can go obsolete and be delisted and no longer certified. If that is the case, then we can find a suitable replacement with the same ratings, and certified/approved to the same standards as the original part/assembly. Depending on the nature of what the product does, it may require additional review by the safety engineer and possibly depending on the ratings may require some inspection and testing.
- For the EU market and associated partners, the CE mark requirements states that the manufacture create an EU Declaration of Conformity (DoC) for the product or series of products being put into the EU markets. NeuronicWorks Inc. can determine the list of applicable EU directives, show the applicable EN xxxxx standards that were tested by the accredited laboratory. We will ensure that DoC is signed and dated by a person responsible for regulatory compliance and certification for the product or series of products.
NeuronicWorks Inc. can also review instruction/installation manuals and user guides to ensure all related safety and emissions requirements are present. For instance, we will make sure that the certification information, Safety precautions or other safety requirements in the standard are present with the proper terms and proper language for the country (or countries) where it will be used.
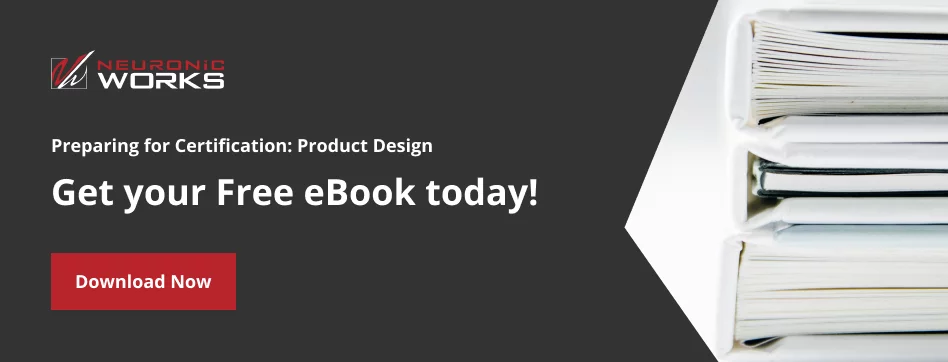