Are you looking for a comprehensive turnkey solution for your product development requirements? NeuronicWorks offers both design and manufacturing services that will ensure your product reaches market more efficiently and seamlessly.
Product Manufacturing: Design Transfer
Manufacturing is a critical part of the PLC (product life cycle) for any given product. Product innovators and some young product designers, miss considering the manufacturing aspect from the initial design stage and then get saddled with issues that result in costly redesigns and significant delays.
As popularly quoted by Elon Musk, “The difficulty and value of manufacturing is underappreciated. It's relatively easy to make a prototype but extremely difficult to mass manufacture […] reliably at scale.”
Manufacturing a product requires significant investment in space, equipment and personnel to efficiently, effectively and repeatedly build products. There are also well-established processes that mitigate risks in design transfer from prototypes to full scale production to get a successful and profitable product.
To better understand the process, let’s start by reviewing the main phases involved in manufacturing and then focus on specific aspects of this flow as graphically listed in Figure 1.
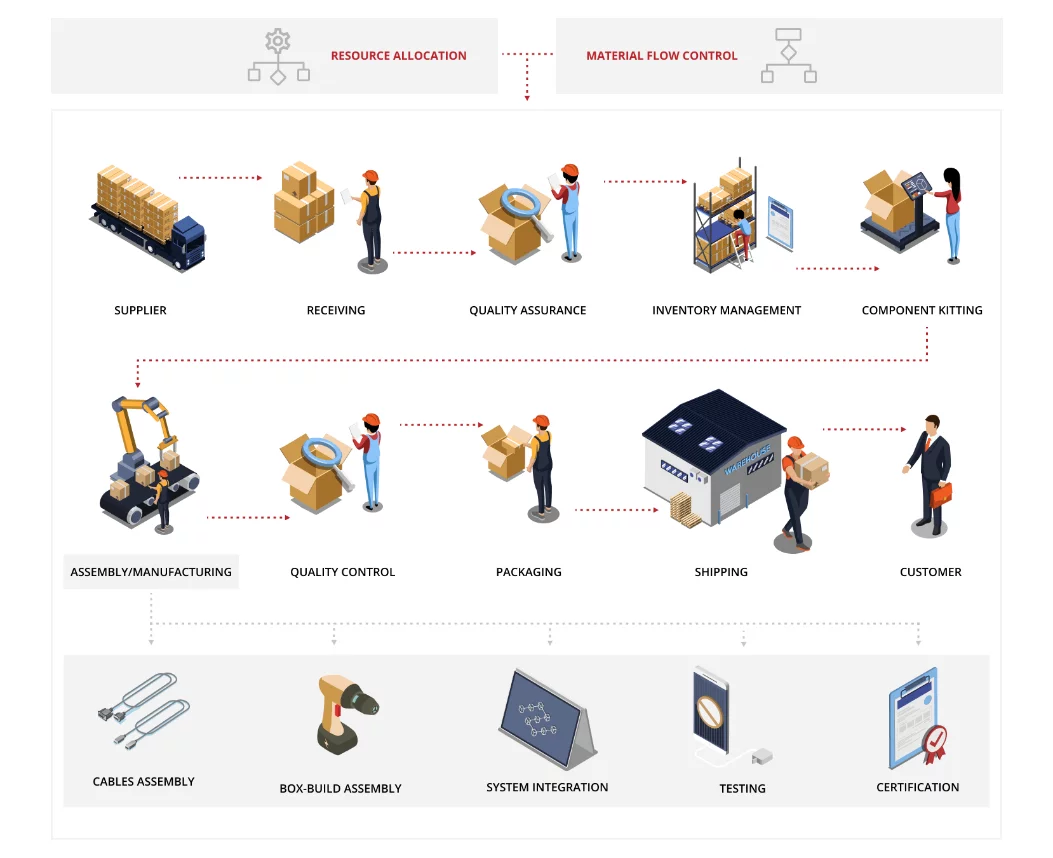
Figure 1: Main stages of the manufacturing process
- Source (procurement) raw materials and components from suppliers
- Once the BOM (Bill of Materials) is created by the engineering department, the procurement of necessary components can commence.
- Receiving and incoming Quality Assurance
- Incoming quality inspections verifies that the delivery matches the purchase order, in terms of quantity and quality. It additionally inspects to ensure there are no damages, and to check if components are within specs and tolerances. The inventory system is updated accordingly, and the components are stored in the warehouse.
- Inventory Management
- Inventory management is responsible for ordering, storing and tracking stock as available in the warehouse
- Resource Allocation
- It is the process in which resources are efficiently allocated for production. Resources can be components, machinery, labour, technology among others.
- Material flow control
- Material flow is a sub-area of logistics that includes the storage, packaging and movement of goods of all kinds within a company. The movement of goods is regarded as an internal material flow.
- Components Kitting
- Kitting, an internal warehouse operation, is the process of gathering and grouping, production ready electro-mechanical components required to manufacture a predefined quantity of product. This allows for a more efficient and streamlined process of production, inventory tracking and even packing and shipping.
- Assembly/Manufacturing
- Electrical and electronic systems contain a variety of electro-mechanical components and subassemblies. The process of integrating these components into an enclosure or panel is referred to as a box-build or system integration. It can range from simple to complex type depending on its purpose and production specifications. Typically, it will include installing all the necessary components and subassemblies as well as routing the wires and cables. A box-build may even include fabricating or procuring the enclosure or panel.
- Quality Control before shipping
- Outbound Quality control (QC) is a process through which a business seeks to ensure that product quality is maintained. Quality control involves testing units and determining if they are within the specifications for the final product.
- Order picking
The order picking or order preparation operation is a logistic warehouse process. It consists in taking and collecting articles in a specified quantity before shipment to satisfy customers orders. It is a basic warehousing process and has an important influence on supply chain's productivity. This makes order picking one of the most controlled logistic processes. It is one of the warehouse management system functionalities .
Now that we have a basic understanding of the processes involved in manufacturing a product, let’s take a closer look at one of the specific aspects of the flow that can help mitigate the risk of transferring prototypes to full scale production and to be more specific, the documentation required to smoothly transition from design to manufacturing.
As mentioned in the beginning of this blog, it is important to consider manufacturability and producibility of a design, early in the design stage to ensure successful design transfer to production.
At NeuronicWorks Inc. (NWI), our manufacturing engineers are involved in reviewing the Product Requirements Document (PRD) as early as in the initial stage of design, participating in Design for Manufacturing and Design for Test meetings.
The design team factors in the feedback of the manufacturing engineer and goes through a detailed design process to finally bring about a working prototype.
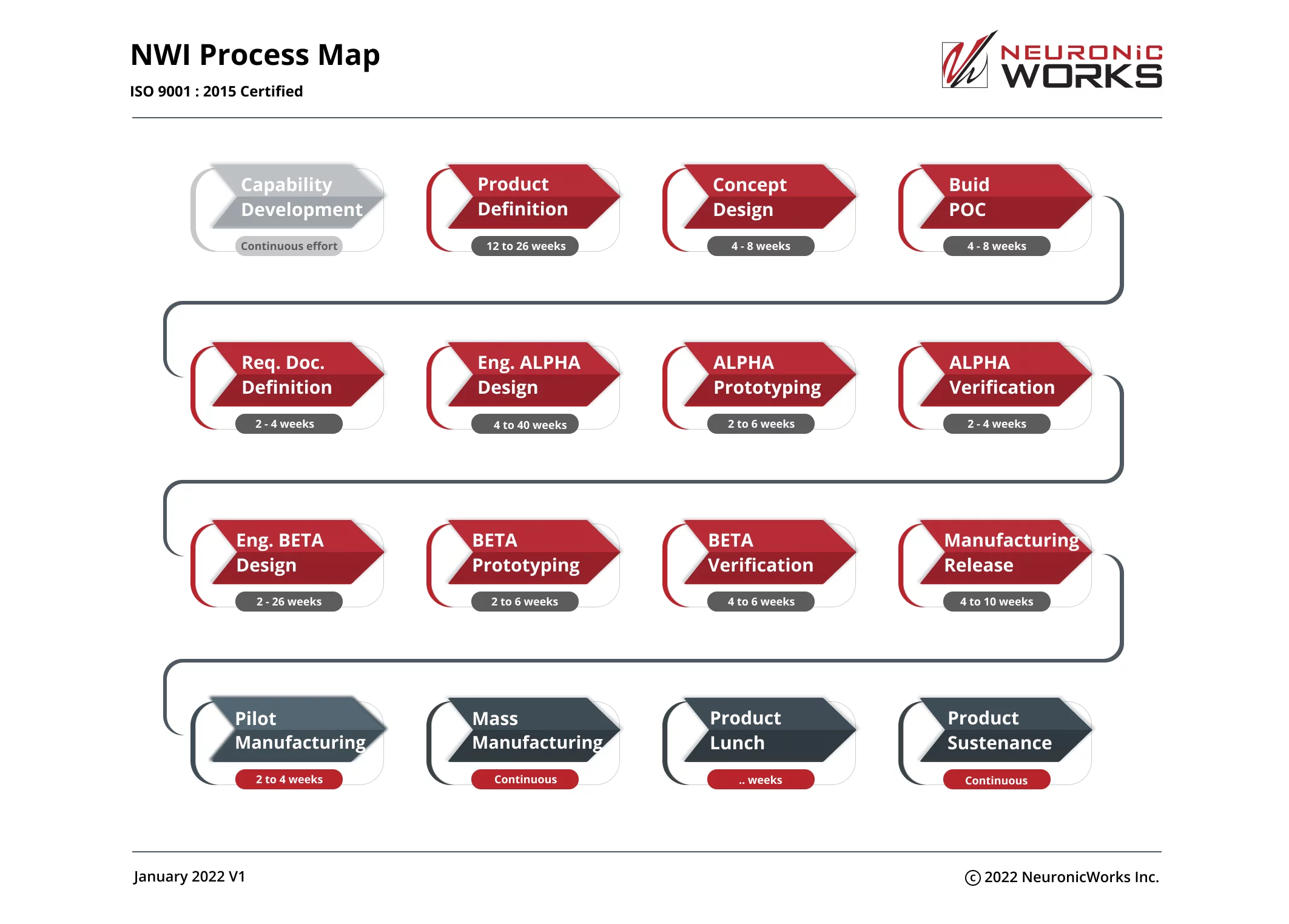
Figure 2: NWI Process Map
Once the prototype is completed by our engineering team and validated by our QA department, a Production Readiness Review (PRR) commences producing the following documentation:
- Manufacturing Build Package (MBP),
- Inspection Guidelines for Quality Control, and
- Manufacturing and Safety Certification.
The next step in our process, is to build the Pilot units (or First Article). The pilot units are built by our manufacturing department following the documents in the Manufacturing Build Package provided by the design team.
The Manufacturing Build Package includes:
- BOM (Bill of Material),
- Assembly Instructions,
- Test Instructions,
- Drawings,
- Schematics,
- Quality Control Checklists,
- Packing and Delivery Instructions
During the entire process of building and testing the Pilot, any correction or improvement ideas for the manufacturability of the product is done through the CAPA (Corrective and Preventive Actions) system. Corrective actions are actions taken to eliminate the causes of non-conformities or other undesirable situations, to prevent recurrence. Preventive actions are actions taken to prevent the occurrence of such non-conformities, generally as a result of risk analysis.
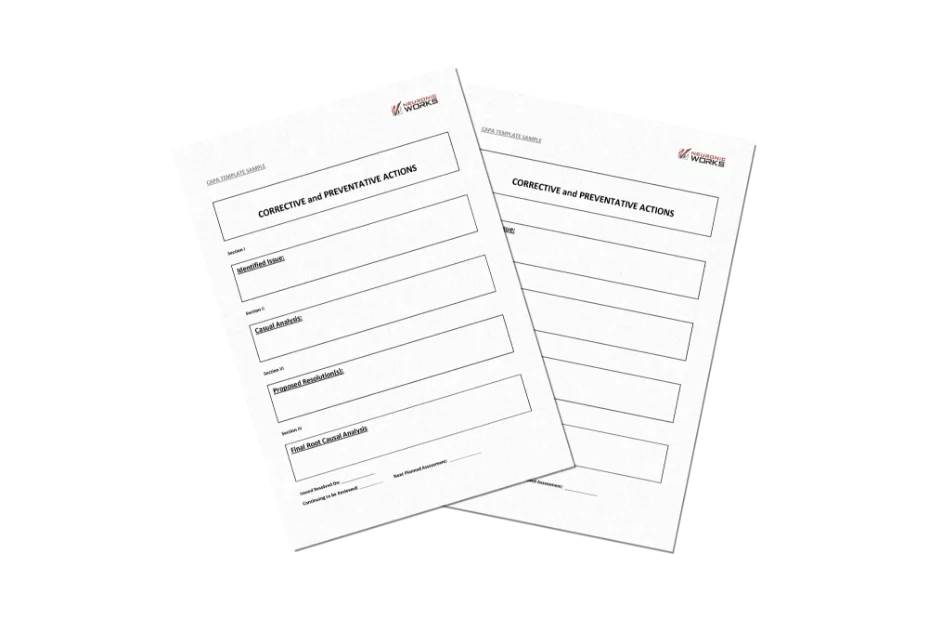
Figure 3: Reference CAPA Template
Once the Pilot is completed and before Full-Scale Production begins, another step takes place: Manufacturing Process Validation.
This process is meant to analyze and review all the CAPA entries, and other findings and recommendations that have come about during the pilot build. In this stage the manufacturing process design is assessed to confirm that the process performs as expected and can meet determined manufacturing standards. Critical quality attributes are evaluated, and critical process parameters are taken into account to confirm product quality.
Based on the results of the Manufacturing Process Validation, the Manufacturing Build Package is updated, revised, approved and released to the Manufacturing Department for full production.
Once commercial production is in process, all completed goods are closely inspected manually and by machines, before moving into packaging, shipping and delivery process.
One of the most significative advantages of NeuronicWorks is our vertical integration. Here at NeuronicWorks, an ISO 9001:2015 certified company, projects are seen right through from initial design stage to prototyping, testing and certification, sourcing components and inventory management, pilot and low-volume manufacturing, shipment & logistics.
The newly expanded facility with state-of-the-art equipment will be able to significantly increase production rates and offers the ability to handle larger, more complex projects seamlessly out of one location.
Having the design team and manufacturing facilities under one roof, using the same ERP system, processes and procedures, decreases the time needed from design to final product delivery. It also provides a closed loop feedback system from the manufacturing back to the design team saving on time and increasing efficiency. This is feedback that will improve the design quality with each New Product Introduction (NPI).